
PLMとは何? 機能や導入のメリット、PDMとの違いを徹底解説
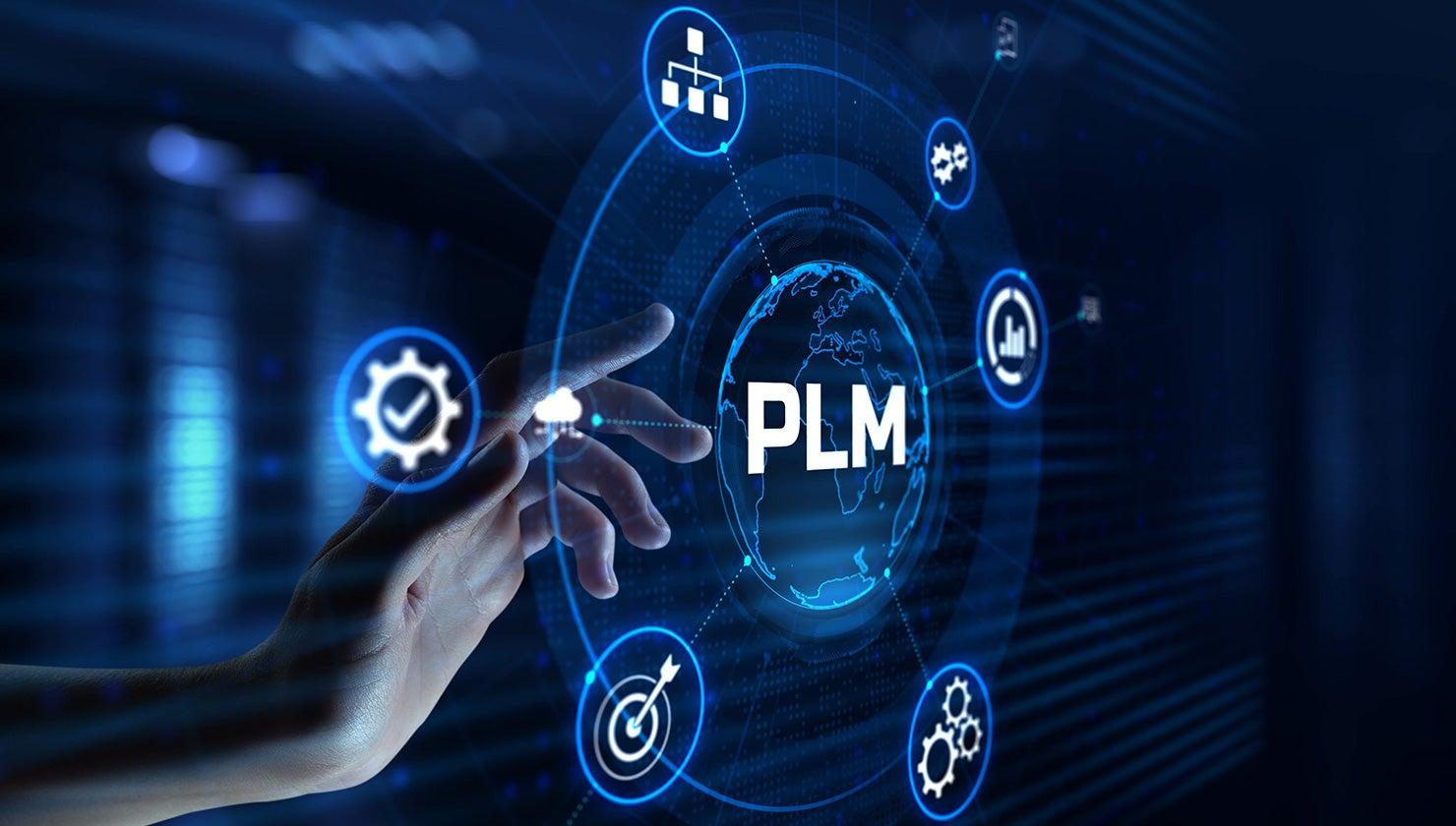
製造業の現場では、デジタル技術を用いて業務プロセスの改善を図るDX化が進み、さまざまな取り組みが行われるようになりました。そうしたなかで、業務の効率化や利益拡大に役立つ手段として注目されているのが「PLM」です。この記事では、PLMの概要や機能、メリット、導入時の注意点などをご紹介します。また、PLMと深い関係にある「QCD」の概要や、混同しやすい用語である「PDM」との違いも併せて解説していきます。
PLMとは?
製品が企画、設計・開発、製造、販売といった過程を経て保守や廃棄の段階に入り、市場を退場するまでの一連のプロセスを「製品ライフサイクル」と呼びます。PLM(Product Lifecycle Management)とは、この製品ライフサイクル全体をまとめて管理するために用いられる手法やシステムを指す言葉です。
PLMという概念は、1990年代にはすでに存在していたといわれています。その後、2000年代にコンピューターが急速に普及したことで、製造業の現場においてもデジタル技術の活用が進み、PLMの注目度が高くなりました。PLMによって情報を一元化すれば、各プロセスの技術情報や知識が集約され、高品質な製品を低コストで効率的に製造できます。
PLMへの取り組みでQCDの向上が実現可能
PLMへの取り組みには、製品開発で重視すべき「QCD」の向上が見込めるというメリットがあります。QCDとは、「品質(Quality)」「コスト(Cost)」「納期(Delivery)」の頭文字を取った言葉です。ここでは、QCDを構成する3つの要素について詳しくご紹介します。
品質:Quality
品質の向上は、顧客からの信頼の獲得や顧客満足度の向上につながるため、QCDの中でも特に重要な要素です。
情報通信技術の発達に伴い、顧客が製品に関する情報を容易に得られるようになったことで、製品の品質に求められるハードルは年々高くなっています。PLMのような手法を用いることで、顧客からの意見を製品ライフサイクルに取り入れやすくなり、迅速に品質をアップデートしていくことが可能になります。
コスト:Cost
QCDにおけるコストとは、製品の開発や製造、完成品の運搬、メンテナンスなどにかかる費用や時間を指します。また、これに伴う人件費や材料費もコストに含まれます。コストをむやみに減らすと、品質や納期に悪影響を及ぼすため、コスト削減を目指す際は適切なバランスを保つことが重要です。
納期:Delivery
製品を企画してから顧客に提供するまでの期間は、短縮すれば顧客満足度の向上が期待でき、遅れれば顧客からの信頼を失う恐れがあります。だからといって納期を短縮し過ぎると、品質低下につながる可能性もあります。PLMによってプロセス全体の状況を把握したり、顧客の意見を分析したりすることで、最適な納期を見極めることができます。
PLMと似ているPDMとは
PLMと混同されやすいものに「PDM」があります。PLMとPDMは、どちらも製品開発に関わる情報の管理を支援するツールです。しかし、両者は管理する範囲や目的、成り立ちなどがそれぞれ異なります。ここではPDMの特徴と、PLMとの違いについて解説します。
PDMの概要
PDM(Product Data Management)は、製品開発に関するさまざまなデータを一元管理することを目的としたツールです。デジタルで製品開発のプロセスを管理する手法の一つとしてPLMより一足早く誕生し、1990年代にはさまざまな企業で導入されていました。
PDMで扱われるデータには、設計図となるCADデータやBOM(部品表)、仕様書、図面、エンジニアからの情報を伝達する技術ドキュメントなどがあります。設計開発部門が持つこれらのデータを統合し、ほかの部門に共有することで、生産プロセス全体の効率化を図ることがPDMの主な目的です。データの一元管理や情報共有のほか、データの検索と再利用、ワークフローの管理などが行えます。
PDMが普及した理由・背景
製造業では、1980年代後半からデジタル化された設計ツールが普及し始め、CADツールという設計用のソフトウェアが導入されるようになりました。その結果、大量のデジタルデータを管理する必要性が出てきたことから登場したのが、PDMという概念です。PDMは設計データの効率的な利用を実現し、QCDの向上に貢献してきました。
PLMとPDMの違い
2000年代に入ると、顧客ニーズの多様化に伴い、これまで通り設計データを共有するだけでは企業競争力の確保が困難になりました。こうした時代の変化に対応できるようPDMが進化していった結果、登場したのがPLMです。
PDMは設計業務の効率化に特化した仕組みになっていたのに対し、PLMは製品ライフサイクル全体にまで管理する範囲が広がっていることが、両者の主な違いです。
PLMで管理される内容には、生産設備や人員、流通、ユーザーサポートに関するデータのほか、PDMで管理されていた設計業務のデータも含まれます。情報を一元管理する範囲が広がったことで、QCDのバランスをよりよい形で改善し、企業競争力を高めることが可能になりました。
PLMの手法を用いたツールは「PLMシステム」と呼ばれます。各部門の業務をサポートする複数のソフトウェアなどで構成されており、幅広い機能に対応可能です。代表的な機能として、以下のようなものがあります。
コラボレーション開発
設計データや仕様書、部品表などのあらゆる製品データの一元管理は、PLMシステムの中核ともいえる機能です。
製品の開発プロセスのなかで生まれる情報や帳票は、膨大な数になるうえに、それぞれの部門にバラバラに存在しています。たとえば部品表なら、製品を構成する部品のほか、梱包材や補助材、メンテナンスに必要な部品など、各工程の情報が必要になります。PLMシステムは、企画段階から保守まで一連の情報を一元化することで、こうした部品表の管理を容易にします。
集約された情報の更新や検索も可能なため、「参照したい情報が見つからず問い合わせに時間がかかる」「誤って古い情報を使ってしまう」といった事態も防げます。また、各部門で蓄積したノウハウの活用を促進することにもつながります。
チーム間の連携強化
製造業の業務は、「設計開発」「生産準備」「調達」といった部門や、「メカ」「エレキ」「ソフト」といった設計領域に分かれており、各チームが物理的に離れた場所に拠点を持っているケースもあります。しかし、製品の品質を保ちながら効率的に開発を進めていくためには、部門や領域の壁を越えた連携が欠かせません。
PLMシステムには、デジタル化されたワークフロー管理により、このような部門間などの連携をサポートする機能があります。開発段階で設計に変更などがあった場合は、リアルタイムに生産技術担当者と連携をとり、スピーディーに影響範囲を把握することが可能です。さらに、変更履歴の追跡や、日常的な業務プロセスの自動化も行えます。
これらの機能を活用すれば、場所を問わずスムーズに、各チームが並行して作業を進められます。
プロジェクトの管理
プロジェクトに関わるチームがスムーズに連携するためには、それぞれの作業状況が不透明になることを避ける必要があります。また、どこかで進捗の遅れやトラブルが発生した場合には、全体のスケジュールへの影響を的確に把握し、できるだけ早く対策を取らなければなりません。
PLMシステムにはプロジェクトを管理する機能があり、全体の進行状況やリソースの使用状況を監視できます。リアルタイムで状況を確認できるため、問題が起きた際も素早い対応が可能です。効率的に業務を行うことで収益の最大化を目指すPLMにとって、開発スケジュールの最適化は重要な機能の一つといえます。
そのほか、原価やリソースの管理を行うことや、QCDの達成状況や課題について把握することも可能です。こうした機能を生かしてプロジェクト全体を細やかに管理することで、QCDをバランスよく向上させられます。
PLMシステム導入によるメリットとは
PLMシステムの導入によって製品ライフサイクルの一元管理を実現すれば、次のようなメリットを得ることができ、QCDを向上させられます。その結果、顧客からの信頼の獲得や、製品の競争力アップにもつながります。
製品の品質が向上
PLMシステムの導入で部門間の連携がスムーズになることで、設計変更やミスの修正が必要になった際に素早く対応できます。また、各工程の情報が統合されていると品質の一貫性を保ちやすく、品質改善のためのデータ分析も行いやすいです。製品品質の向上は、不良品やリコールを減らすことにもつながります。
コストを削減
各工程の詳細なデータを可視化できるため、人件費や原材料費、発注ミスの有無などを総合的に把握し、コスト削減に役立てることが可能です。得られたデータを蓄積していけば、新たな製品開発を行う際のコスト管理にも応用できます。リアルタイムな情報伝達と業務のデジタル化を実現できるため、作業時間の短縮による人件費削減も見込めます。
業務効率が向上
PLMシステムを導入すると、見積書の計算や手書き図面のデータ化といったあらゆる業務が自動化され、情報はシステム上で一元管理されるようになります。そのため、アナログ業務に付随する細かな手間や手戻りはなくなり、必要な情報を探し出したり製造工程全体の見直しを行ったりすることが容易になるため、業務効率が格段に向上します。
PLMシステムを導入する際の注意点
PLMシステムが正しく本来の力を発揮するためには、製品ライフサイクルに関するすべての情報を集約することが重要です。「既存のシステムとの相性が悪く、連携ができない」などの問題により、集約されない情報が発生した場合、導入効果は薄れてしまいます。導入するPLMシステムを選定する前に、既存システムとの連携について確認しておくことが大切です。
また、自社の業務プロセスとシステムの機能がマッチしているかどうかや、拡張性やカスタマイズ性についても調べた上でシステムを選定すると、より効果を発揮しやすくなります。機能の拡張や既存システムの改修を検討する場合は、追加のコストが発生するため、費用対効果についても事前に確認しておくことが推奨されます。
先に自社の直面している状況や課題の洗い出しをしておくと、こうした事前確認をスムーズに進められます。それでも導入や運用にあたって懸念が残るようであれば、PLMシステムに詳しい企業にサポートを依頼するという手段もあります。
まとめ
製造業のDX化を語る上で欠かせないPLMについて、概要やPDMとの違い、機能の詳細、導入するメリットと注意点などをご紹介しました。
適切な形でPLMシステムを導入・運用し、製品ライフサイクルに関わる情報を一元管理する仕組みを実現できれば、QCDの大幅な改善が見込めます。アナログな管理方法から脱却し、収益の最大化を目指したいとお考えの際は、ぜひ今回ご紹介した内容を参考にしてみてください。